Industry Insight: Pipeline Coatings
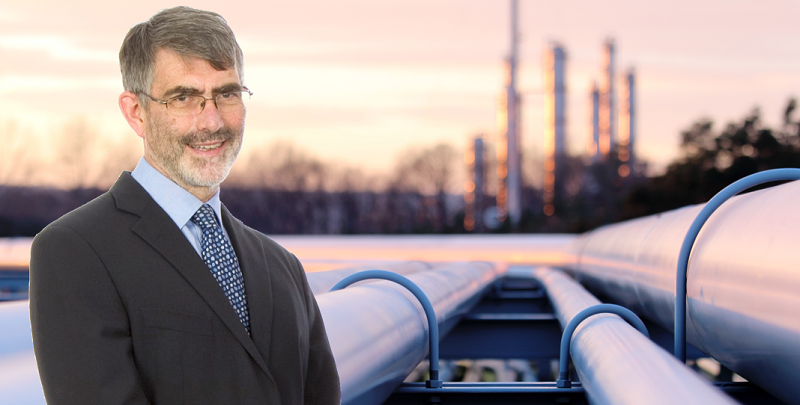
Pipelines constitute a major infrastructure investment for transporting materials. In the event of failure, they can cause significant loss to the owner and serious potential for environmental damage.
AGM’s Technical Director, William Weaver, offers an insight into the importance of pipeline protection and the role that nanomaterials like graphene can play in the development of advanced corrosion protection systems.
Pipelines represent a major infrastructure investment, frequently carrying materials which, in the event of failure, can cause significant losses to the owner, negative impact on downstream supply chains and even serious potential for environmental damage.
To fulfil their role, pipelines often run long distances either underwater or underground. This physical challenge is often further complicated by the crossing of international borders. Coatings are essential to the protection of pipelines from corrosion and subsequent failure but are themselves subject to degradation by severe abrasion, hydrothermal ageing and chemical attack.
Graphene was first isolated in 2004 at the University of Manchester, an event which was followed by the Nobel prize for Physics in 2010. One of the many remarkable properties of graphene is its impermeability to gases. Graphene nanoplatelets (or GNPs) offer a cost-efficient and scalable alternative for use in barrier systems. Through the dispersion of GNPs into epoxy, it has been observed that low level additions of GNPs offered improved barrier properties to reduce the risk of corrosion and increase chemical resistance.
AGM’s GNPs are manufactured using the Company’s patented proprietary ‘bottom up’ process, yielding high specification graphene materials. We produce a range of GNP dispersions capable of addition into coating systems and has undertaken significant development activity to demonstrate their use in paints and coatings, enabling increases in barrier performance giving improved corrosion and chemical resistance performance.
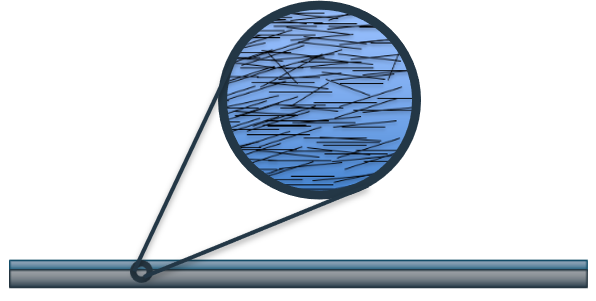
In addition to the benefits of adding graphene in to the base primer coat in a pipeline protection system, AGM has also shown that the introduction of GNPs into the intermediate coat or “Tiecoat” can significantly increase the impedance of a protective coating system as measured by electrochemical impedance spectroscopy (EIS) when studied in conjunction with neutral salt spray testing (ASTM B117).
This, therefore, enhances the protection of the pipeline further by extending the life of the existing primer coat.
Recently it has been demonstrated that GNPs, when incorporated into an organic coating system, provide protection, via a highly tortuous path, which acts to impede the movement of corrosive or other chemical species towards the metal surface, creating a passive corrosion and chemical resistant protection mechanism.
In support of this, previous work has also shown that very small additions of GNPs decreased water vapour transmission rates, indicating a barrier type property, as shown in figure 1.
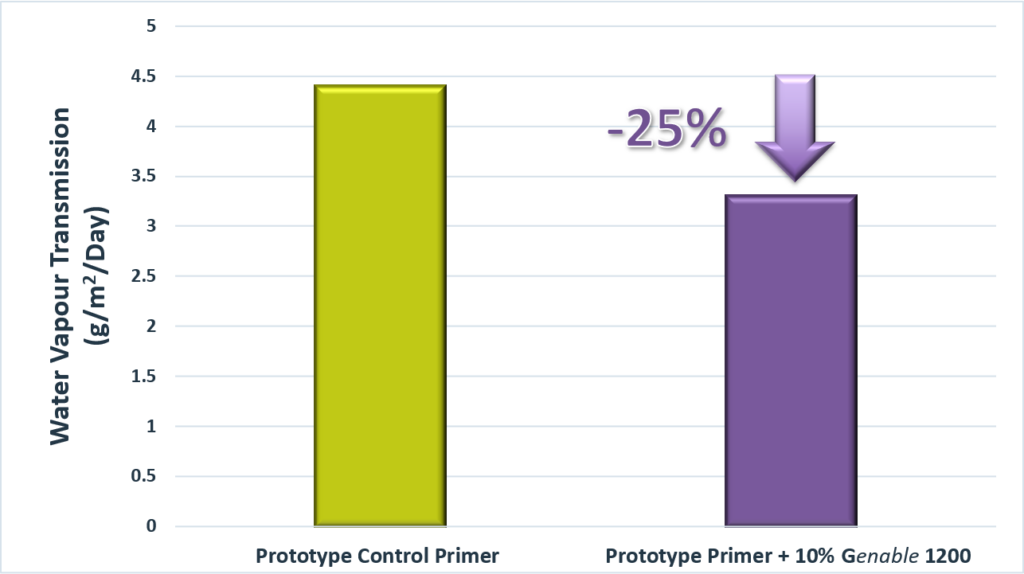
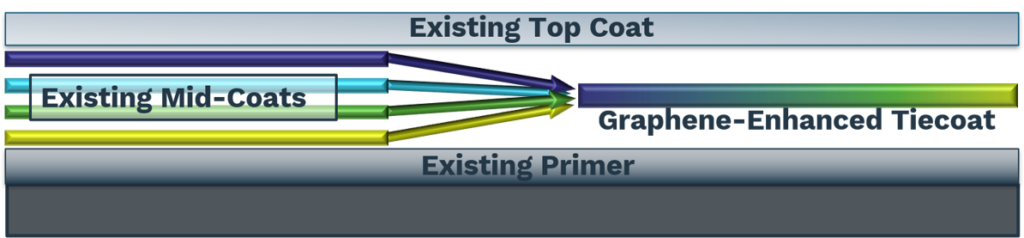
The choice of a coating system for pipelines is influenced by a number of criteria, from performance, location and coating life expectancy to geographical regional factors such as regulatory requirements and climate. However, all pipeline coatings need to meet a few critical requirements of coatings:
- Excellent coating adhesion to the pipe substrate.
- Low permeability through the coating.
- Resistance to cathodic disbondment.
- High electrical resistance.
Typical coating systems for pipeline application are frequently based on high build epoxy or polyurethane chemistry. Such systems often utilise additive materials to increase both corrosion and chemical resistance protection. Graphene modification can easily be incorporated into such epoxy or polyurethane systems through the use of AGM’s Genable graphene nanoplatelet dispersions.
Graphene in this way offers potential for real-world application in pipeline systems and an innovative solution to enhance corrosion and chemical resistant coatings.